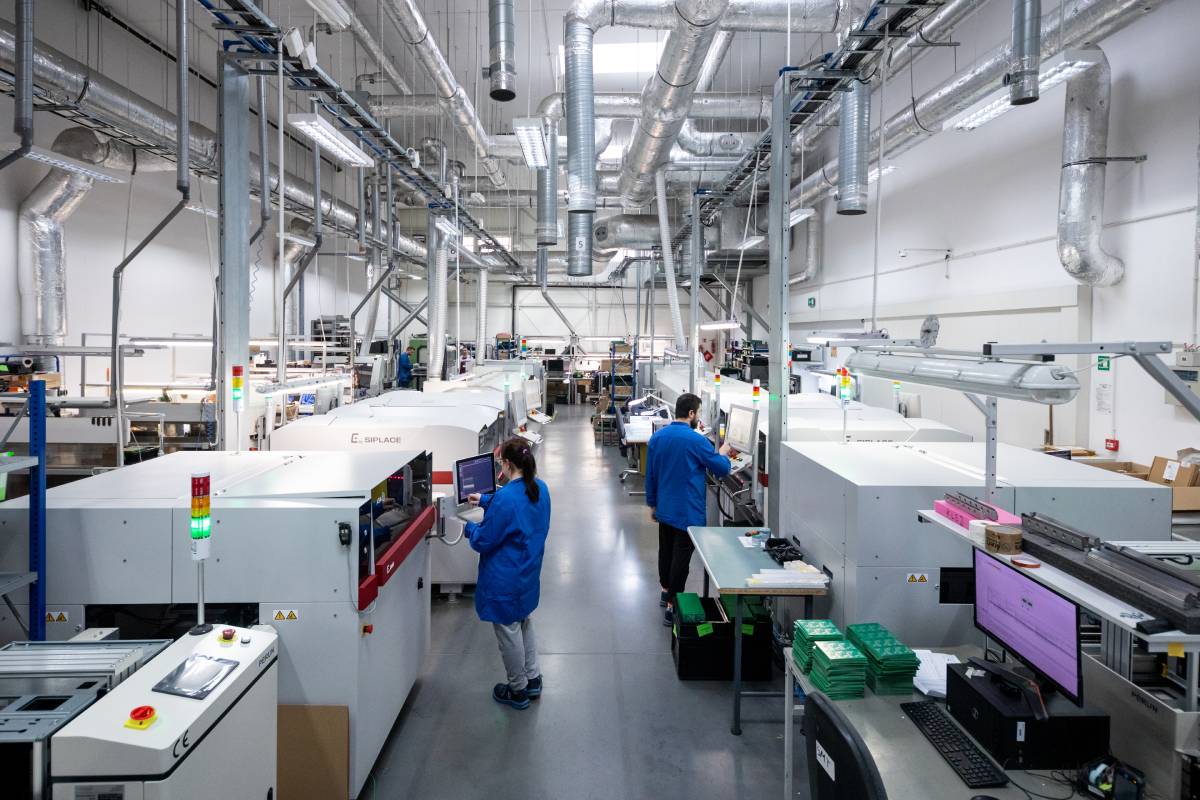
Lean Management is a production and process management philosophy that focuses on eliminating waste, optimizing resources, and continuous improvement. It is based on the principle of delivering value to the customer while minimizing unnecessary actions and costs. Key to Lean Management is streamlining workflows, reducing excessive inventory, and eliminating inefficiencies.
The concept of Lean Management originated in the Japanese automotive sector and is directly linked to the Toyota Production System (TPS). After World War II, Toyota, under the leadership of Taiichi Ohno, developed an innovative approach to manufacturing based on flexibility, waste elimination, and continuous process improvement. TPS allowed Toyota to achieve exceptional production efficiency and quality, which contributed to the company’s global success.
For many years, TPS remained unnoticed outside Japan, mainly due to the lack of formal documentation. It wasn’t until the 1980s and 1990s that this system began to be studied and implemented worldwide. A key moment was the 1990 publication of the book The Machine That Changed the World by James Womack, Daniel Jones, and Daniel Roos, which compared the efficiency of manufacturing plants in various countries and highlighted TPS as the most effective production management model. The term "Lean Production" was introduced by John Krafcik in 1988 to differentiate TPS from traditional mass production, which is characterized by large inventories and buffers in processes.
Lean Management is based on several fundamental principles aimed at optimizing processes and eliminating waste:
Lean Management utilizes a range of tools to support the optimization of production processes, including:
Implementing Lean Management requires the engagement of the entire organization and a shift in work culture. The key stages of implementation include:
At Novatronik, we focus on a modern approach to work organization that allows us to achieve better results and increase competitiveness.
We have implemented proven management methods, such as 5S and Kaizen, which help us maintain high product quality, process efficiency, and safety.
By consistently applying these principles, we eliminate unnecessary waste, optimize resource utilization, and engage employees in the continuous improvement of daily work.
Our goal is to continuously raise standards, which translates into better products, higher customer satisfaction, and the stable growth of the company.
At Novatronik, we have implemented the 5S methodology, which helps us maintain order, improve workplace ergonomics, and increase production efficiency.
The key elements of this system are:
Consistent application of Lean Management principles at Novatronik leads to higher efficiency, reduced waste, and better quality final products.
The Kaizen philosophy is one of the pillars of our development strategy. We encourage employees at all levels of the organization to suggest small but specific improvements that contribute to process optimization.
As a result, we achieve:
By combining 5S and Kaizen, we continuously improve our processes, increasing competitiveness and customer satisfaction.
Lean Management is an effective production management strategy that enables cost reduction, waste elimination, and increased operational efficiency. The combination of Lean with Industry 4.0 technologies allows companies to achieve even higher levels of optimization, improving quality and competitiveness in the market.