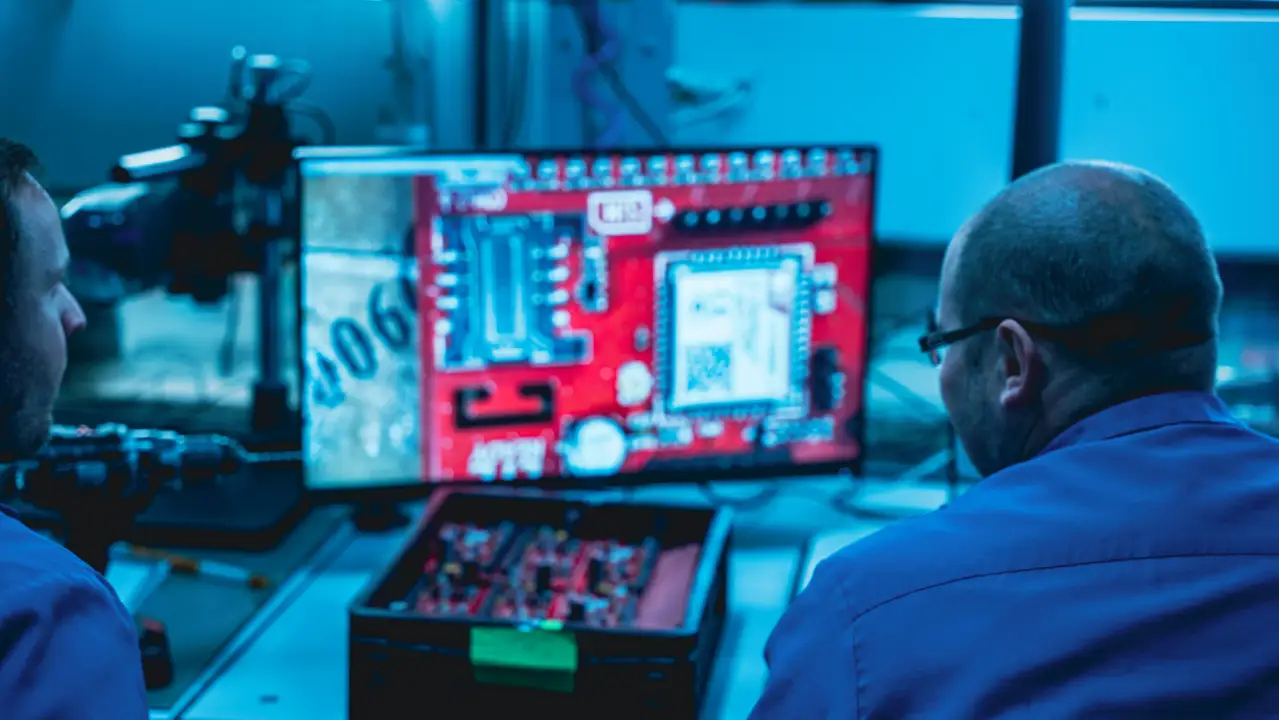
W procesie projektowania kluczowe jest uwzględnienie zasad, które pozwolą uniknąć problemów na etapie produkcji, zapewnią bezawaryjność urządzenia oraz umożliwią optymalizację kosztów. Konstruktor powinien zwracać uwagę na aspekty technologiczne, dostępność materiałów oraz inne czynniki, aby finalny produkt był nie tylko funkcjonalny i trwały, ale także ekonomicznie opłacalny, a cały proces produkcji przebiegł bez zakłóceń.
Decyzja o wyborze technologii montażu elektroniki, takiej jak montaż powierzchniowy (SMT) , montaż przewlekany (THT) lub montaż hybrydowy, jest kluczowa w procesie produkcji, a jej dobór zależy od wielu czynników. Wybór ten ma wpływ na wytrzymałość mechaniczną połączeń, wydajność procesu produkcyjnego oraz koszty produkcji.
Montaż SMT to technologia montażu komponentów bez nóżek, które są lutowane bezpośrednio do powierzchni płytki drukowanej (PCB). Jest idealna do produkcji masowej, zwłaszcza w przypadku małych i średnich komponentów, które można łatwo umieścić za pomocą automatycznych maszyn. Daje to możliwość uzyskania wysokiej gęstości komponentów na płytce.
Z kolei montaż THT (przewlekany) wykorzystuje komponenty, które posiadają nóżki, które przechodzą przez otwory w PCB i są lutowane na drugiej stronie płytki. Ta technologia jest bardziej odpowiednia dla większych komponentów oraz tych, które wymagają większej wytrzymałości mechanicznej. Montaż THT jest częściej wybierany w produkcji prototypowej lub w przypadkach, gdzie komponenty muszą wytrzymywać ciężkie warunki pracy.
Montaż hybrydowy, który łączy technologie SMT i THT, jest stosowany, gdy projekt PCB wymaga połączenia zalet obu technologii. Może być przydatny w produkcji urządzeń, które łączą zarówno małe, delikatne elementy, jak i większe komponenty o większej wytrzymałości.
Aby montaż elektroniki przebiegł sprawnie i bez błędów, kluczowe jest odpowiednie zaplanowanie układu komponentów na PCB. Dobry projekt to podstawa nie tylko do prawidłowego montażu, ale także do późniejszej testowalności i wydajności urządzenia.
Przede wszystkim należy pamiętać, by komponenty SMT były ustawione w odpowiednim kierunku produkcji, co ułatwia automatyczne lutowanie. Komponenty THT powinny być oddzielone od obszarów przeznaczonych do lutowania SMT, aby uniknąć błędów montażowych.
Ponadto ważne jest, aby zaprojektować przestrzeń na chłodzenie oraz na ewentualne testy, które mogą wymagać dodatkowego miejsca na płytce. Dzięki odpowiedniemu układowi komponentów można zminimalizować ryzyko awarii i poprawić efektywność procesu produkcji.
Minimalne odstępy między komponentami na PCB mają kluczowe znaczenie dla jakości montażu. Zbyt małe odległości mogą prowadzić do zwarć oraz trudności z chłodzeniem komponentów. Ważne jest, aby zaplanować odpowiednią przestrzeń na montaż automatyczny, co umożliwi precyzyjne lutowanie.
Optymalizacja odstępów pozwala także na łatwiejszą naprawę w przypadku ewentualnych usterek. Większe przestrzenie pomogą w łatwiejszym dostępie do komponentów w trakcie serwisowania urządzenia. Właściwe zaplanowanie wymiarów i odstępów to kluczowy element wpływający na jakość produktu końcowego.
Projektowanie PCB do wysokoprądowych aplikacji wymaga odpowiedniego dobrania grubości ścieżek oraz szerokości ścieżek, aby zapewnić ich wytrzymałość i stabilność podczas pracy urządzenia. W przypadku komponentów wymagających dużych przepływów prądu, takich jak zasilacze, należy zwiększyć szerokość ścieżek, aby zapobiec ich przegrzewaniu.
Ponadto należy unikać ostrych kątów w ścieżkach, ponieważ mogą one powodować problemy w procesie produkcji i obniżać jakość połączeń. Dostosowanie grubości miedzi oraz odpowiednia konstrukcja ścieżek pozwolą na lepszą wydajność i niezawodność całego układu.
Panelizacja to proces łączenia kilku płytek PCB w jeden większy panel, co przyspiesza proces montażu, zarówno w technologii SMT, jak i THT. Dzięki panelizacji można zmniejszyć odpady materiałowe oraz zwiększyć efektywność produkcji poprzez optymalizację procesu lutowania na fali.
W przypadku produkcji większych serii, panelizacja stanowi istotne udogodnienie, pozwalając na skrócenie czasu produkcji i zmniejszenie kosztów związanych z obróbką każdej płytki osobno. To rozwiązanie jest szczególnie korzystne, gdy zależy nam na wysokiej wydajności i minimalizacji kosztów produkcji.
Projektowanie odpowiednich padów i otworów montażowych to kluczowy etap w procesie tworzenia układów elektronicznych. W zależności od używanej technologii montażu (SMT lub THT) , odpowiedni rozmiar i rozmieszczenie padów mają ogromny wpływ na jakość lutowania i trwałość połączeń.
Montaż powierzchniowy (SMT), który opiera się na lutowaniu komponentów bezpośrednio na powierzchni płytki, wymaga precyzyjnego doboru padów, aby zapewnić ich odpowiednią adhezję. Pady powinny być na tyle duże, by umożliwić skuteczne lutowanie falą lutowniczą, a jednocześnie nie za duże, aby nie utrudniały procesu nakładania pasty lutowniczej. Zbyt małe pady mogą prowadzić do słabej jakości lutowania, a zbyt duże utrudnią precyzyjne ustawienie komponentu.
Montaż przewlekany (THT), w którym elementy przechodzą przez otwory w płytce, wymaga otworów, które są odpowiednio dopasowane do rozmiaru pinów komponentów. Należy unikać zbyt małych otworów, które mogą utrudniać przechodzenie elementów, oraz zbyt dużych, które mogą powodować problemy z lutowaniem, w tym niską jakość połączenia.
Kontrola termiczna w procesie montażu elektroniki zapobiega uszkodzeniom komponentów i zapewnia stabilność układu. Duże różnice temperatur mogą prowadzić do problemów z lutowaniem. Aby temu zapobiec, należy uwzględnić odpowiednie rozmieszczenie masy i wypełnień termicznych.
Zastosowanie pól masy i wypełnień termicznych umożliwia równomierne rozprowadzanie ciepła podczas lutowania. Dla komponentów generujących dużo ciepła warto zaprojektować otwory termiczne, a unikanie różnic w szerokości ścieżek zapobiega niejednolitemu rozkładowi ciepła.
Jednym z kluczowych elementów kontroli jakości w procesie montażu elektroniki jest inspekcja optyczna (AOI). Dobrze zaprojektowana płytka PCB powinna umożliwiać łatwą inspekcję, a także testowanie funkcjonalności komponentów. Projektowanie z myślą o AOI wymaga uwzględnienia odpowiednich punktów testowych oraz przestrzeni do przeprowadzenia inspekcji.
Aby umożliwić automatyczną inspekcję optyczną (AOI), należy zadbać o odpowiednie rozmieszczenie elementów, tak aby nie zasłaniały one krytycznych obszarów, które muszą być inspekcjonowane. Należy również zaplanować punkty testowe dla testów in-circuit (ICT), które pozwalają na sprawdzenie połączeń w obrębie układu już po jego montażu.
Wybór odpowiednich materiałów do produkcji płytki PCB jest kluczowy, aby zapewnić jej odpowiednią trwałość, funkcjonalność i odporność na warunki zewnętrzne. W zależności od wymagań aplikacji, różne materiały będą lepszym rozwiązaniem.
FR4 to najczęściej wybierany materiał do produkcji standardowych płytek PCB, ponieważ oferuje dobry balans między ceną, wytrzymałością a przewodnością elektryczną. Dla bardziej wymagających aplikacji, takich jak elastyczne PCB, lepszym rozwiązaniem będą poliamidy, które zapewniają elastyczność, ale nieco wyższe koszty produkcji. Z kolei dla aplikacji o wysokiej mocy, wymagających lepszej przewodności ciepła, można rozważyć ceramiczne lub metalowe podłoża, które oferują lepsze właściwości termiczne i mechaniczne.
Dobra współpraca z producentem montażu PCB to klucz do sukcesu projektu. Przed rozpoczęciem produkcji warto skonsultować projekt z producentem, aby upewnić się, że pliki Gerber oraz lista BOM są poprawne i zawierają dostępne komponenty, co pomoże uniknąć opóźnień i kosztownych poprawek. Novatronik – Twój partner w produkcji elektroniki
Z ponad 25-letnim doświadczeniem, Novatronik oferuje kompleksowy montaż SMT i THT, dbając o wysoką jakość i terminowość realizacji. Nasze zautomatyzowane linie produkcyjne oraz technologie, jak AOI 3D i X-Ray, zapewniają precyzyjny montaż i pełną kontrolę jakości. Dzięki elastyczności i szerokiej sieci dostawców, dostosowujemy produkcję do potrzeb klienta, optymalizując koszty i czas realizacji.
Chcesz dowiedzieć się więcej o naszych usługach lub omówić swój projekt?
Napisz do nas na novatronik@novatronik.com lub zadzwoń na +48 506 292 460.
Jesteśmy gotowi odpowiedzieć na Twoje pytania i zaproponować najlepsze rozwiązania!
Dokładna dokumentacja jest niezbędna, aby proces montażu przebiegał sprawnie, a połączenia były zgodne z oczekiwaniami. Dokumentacja powinna zawierać precyzyjne dane, które pomogą maszynom montażowym w realizacji projektu.
Do dokumentacji produkcyjnej powinny należeć:
Przed przekazaniem projektu do produkcji należy przeprowadzić szczegółową kontrolę reguł projektowych (DRC), aby upewnić się, że projekt spełnia wszystkie wymagania techniczne i produkcyjne. Sprawdzenie reguł projektowych pozwala wykryć błędy, które mogą wpływać na jakość montażu.
Należy zwrócić szczególną uwagę na:
Przemyślane projektowanie PCB to fundament udanej produkcji elektroniki. Uwzględnienie odpowiednich technologii montażu, staranna organizacja komponentów, dbałość o warunki termiczne i testowalność to kluczowe czynniki decydujące o sukcesie końcowego produktu. Przestrzeganie 12 zasad, o których mowa w artykule, zapewnia optymalizację procesu projektowania i produkcji, minimalizując ryzyko problemów w trakcie realizacji. Współpraca z doświadczonym producentem, takim jak Novatronik, może dodatkowo usprawnić proces montażu i zapewnić najwyższą jakość realizacji.