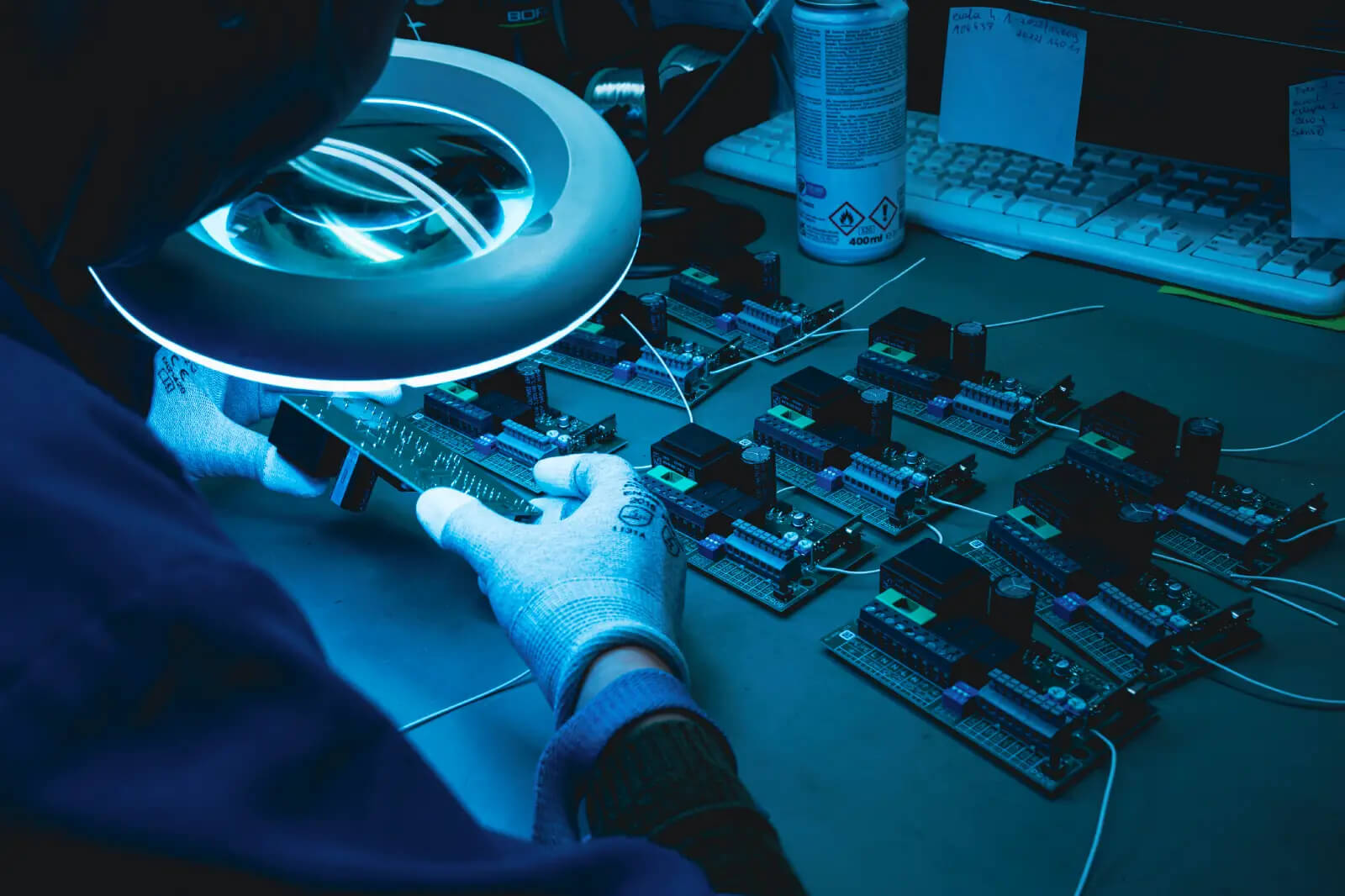
Surface-Mount Technology (SMT) emerged in the 1960s as an innovative method of placing electronic components directly onto the surface of a printed circuit board (PCB). Known initially as planar mounting, SMT quickly gained traction in the 1970s, when pioneering organizations like IBM and NASA integrated it into their advanced designs. This breakthrough enabled the development of far more complex and reliable electronic systems — vital in high-performance mainframes and mission-critical aerospace applications.
The early adoption of SMT marked the beginning of a new era of miniaturization and advanced component integration, paving the way for the industrial-scale production of modern electronics.
A turning point came in the 1980s when SMT began to replace traditional tht assembly at scale. This shift empowered OEMs and EMS providers to significantly miniaturize devices and increase component density. By 1986, surface-mounted components accounted for approximately 10% of the electronic component market — a clear signal of rapid technological advancement.
SMT revolutionized manufacturing by enhancing production efficiency and lowering labor costs through automation (e.g., pick-and-place machines and reflow soldering). Compared to tht mounting, SMT supports smaller components and allows for double-sided PCB assembly, which increases both reliability and design flexibility. As a result, SMT has become the industry standard in sectors such as telecommunications, automotive (including ADAS, infotainment, and vehicle electrification), and consumer electronics.
As of 2023, SMT accounts for over 90% of all electronic manufacturing. Investments are increasingly focused on process optimization, advanced materials (e.g., flexible substrates, conductive inks), and integrating AI into PCB design and fabrication.
Still, THT and SMD technologies coexist. Tht manufacturing remains indispensable in applications that require exceptional mechanical strength or where SMT equivalents are unavailable — such as in aerospace, military systems, and prototype testing environments.
In summary, the transition from THT assembly to SMT has transformed electronics production, improving quality, speed, and scalability. The future of PCB assembly is driven by ongoing innovation in automation and materials science, matching the demands of rapidly evolving industrial and tech-driven sectors.
Through-Hole Technology (THT) is a traditional electronic assembly method in which component leads are inserted through drilled holes in the PCB and soldered on the opposite side. Despite being an older approach, tht mounting is still widely used in designs requiring superior mechanical durability.
Key advantages of THT assembly:
THT and SMT serve different roles: THT is still favored in industries like automotive, aerospace, defense, and prototyping.
Surface-Mount Technology (SMT) is a modern approach where Surface Mounted Devices (SMDs) are directly placed onto the surface of a PCB, eliminating the need for hole drilling. The process relies on automated machinery for precise component placement and reflow ovens for soldering.
Main benefits of SMT:
Challenges of SMT:
SMT dominates consumer electronics, medical devices, computing, and IoT applications — offering unmatched scalability and performance.
Feature | SMT | THT |
---|---|---|
Component Size | Small, compact | Larger |
Component Density | Very high | Low |
Mechanical Strength | Lower | High |
Cost (High Volume) | Low | High |
Cost (Prototypes / Low Volume) | High (initial investment) | Low |
Automation Level | Fully automated | Partially automated or manual |
Repair and Modification | Difficult | Easy |
Common Applications | Consumer electronics, IoT, medical | Automotive, aerospace, military |
Surface-Mount Technology (SMT) dominates PCB assembly due to its capability for miniaturization and increased component density. By placing parts directly on PCB surfaces, SMT shortens electrical paths and boosts device performance. Additionally, SMT’s automation supports rapid mass production and reduces costs — critical for sectors like IoT, automotive, and consumer electronics.
Devices such as smartphones and laptops rely heavily on SMT, with microprocessors and memory modules in SMD packages — designs that are practically impossible with tht assembly.
Despite SMT’s dominance, tht manufacturing remains essential in scenarios requiring rugged mechanical connections and resilience to extreme conditions. THT ensures robust joints by physically anchoring components through PCB holes. It's still the go-to for heavy-duty industrial equipment, defense systems, and medical technology like MRI machines.
THT mounting is also ideal for high-power components such as electrolytic capacitors in PLC controllers, where high temperatures and vibration resistance are critical. While it’s more costly and less suited to miniaturization, THT offers unmatched durability and easier maintenance — crucial in high-reliability applications.
The PCB assembly market is rapidly evolving toward full automation and miniaturization, with SMT (Surface Mount Technology) taking center stage in high-volume manufacturing. Advanced SMD packages like 01005 (0.25 mm × 0.125 mm) are increasingly used in cutting-edge medical devices and consumer electronics, highlighting the growing demand for precision and high-density component placement.
Despite the dominance of SMT, THT assembly (Through-Hole Technology) remains essential in SMT and THT hybrid solutions, where both mounting techniques coexist on the same PCB. This approach allows manufacturers to combine the advantages of both methods — high efficiency from SMT and the mechanical strength of THT. As a result, THT manufacturing still plays a key role in niche applications requiring superior durability and mechanical resistance, especially in prototypes and small production runs.
Choosing between SMT and THT assembly depends on the specific requirements of a project, including functionality, environmental conditions, and intended use.
Modern PCB manufacturing often employs a hybrid strategy, leveraging the strengths of both smt and tht to meet the increasing technical demands of the B2B electronics market.
For companies seeking a reliable electronics manufacturing partner, understanding the differences and complementary nature of THT and SMT technologies is crucial for optimizing both product quality and production cost.